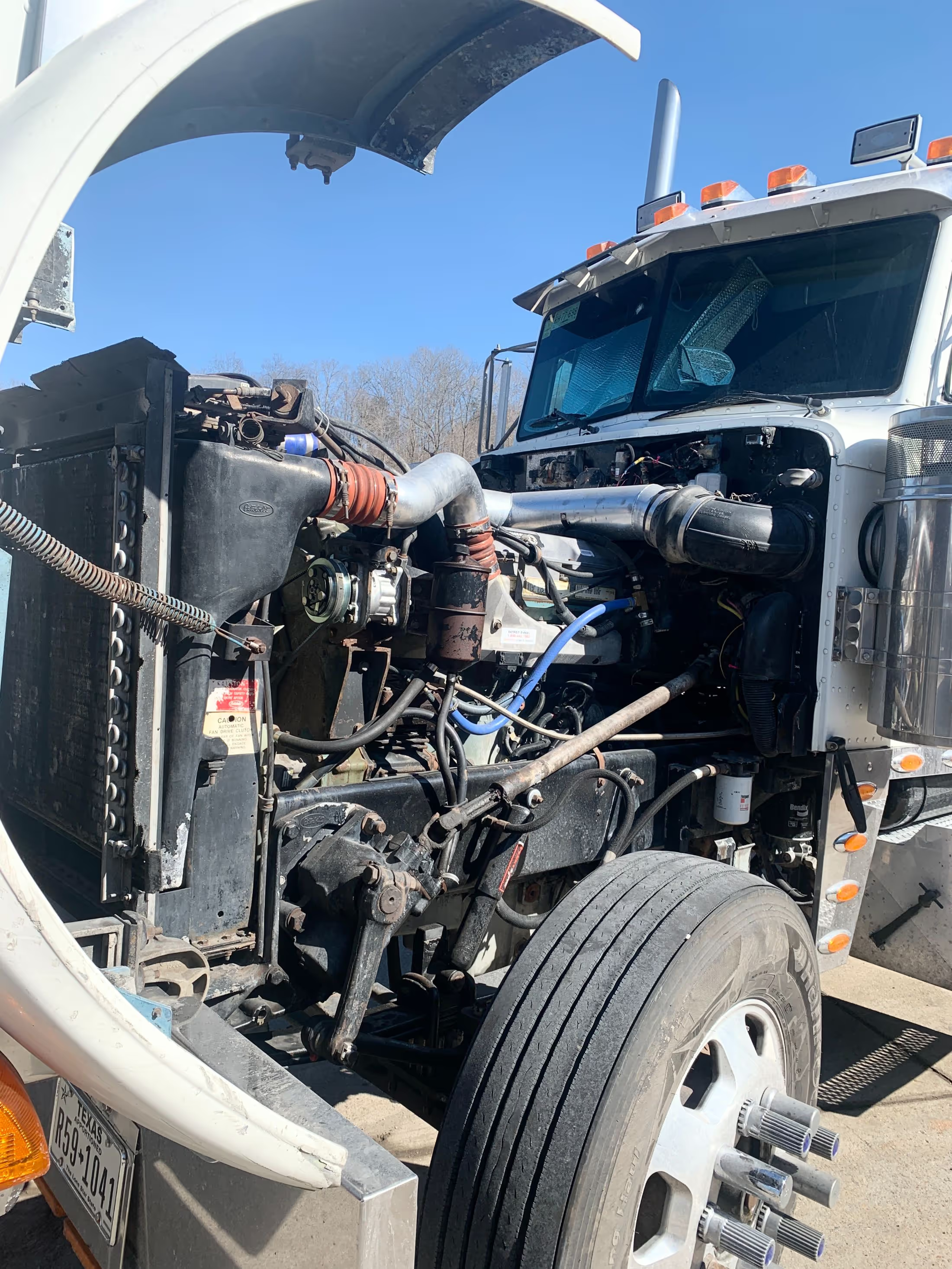
Addressing maintenance challenges in commercial trucks like the Kenworth T470 and T370 models requires an in-depth understanding of their unique features and common issues. For companies operating in and around Houston, Texas, ensuring these trucks are operating efficiently and reliably is crucial for business operations.
The Kenworth T370 and T470 are distinguished by their robustness, versatility, and their role in heavy-duty and medium-duty trucking, respectively. However, their complexity and specific engineering mean they come with their own set of maintenance challenges. This article will explore these challenges and provide insights into how they can be effectively managed.
Kenworth T370: Medium-Duty Versatility
The Kenworth T370 excels as a medium-duty truck, favoured for its adaptability in diverse industries, notable durability, comfort, and fuel efficiency. However, its versatility brings distinct maintenance challenges, especially as it is often used in stop-and-go applications, which can place additional strain on its engine and after-treatment systems.
Engine and Emission Systems
Maintaining your truck’s Diesel Particulate Filter (DPF), Exhaust Gas Recirculation (EGR) system, and other after-treatment components in trucks like the Kenworth T370 presents unique challenges due to the specific driving conditions these vehicles often encounter. These components are crucial for reducing emissions and meeting environmental standards, but their efficiency can be heavily influenced by the type of driving and operational use.
Frequent Short Trips and Low-Speed Operations
Trucks that are predominantly used for short-haul trips or operate primarily in urban settings with lots of stop-and-go traffic may struggle to maintain the optimal functionality of their after-treatment systems. Such conditions prevent these systems from reaching the temperatures required for passive regeneration of the DPF. Without sufficient heat, soot can accumulate in the filter, leading to clogs and decreased performance.
Idling and Light Load Operations
Extended idling or consistently operating under light load conditions can also hinder the effectiveness of after-treatment components. These scenarios fail to provide the necessary exhaust temperatures that are critical for the proper functioning of EGR systems and the DPF's regeneration process. Over time, this can result in soot and particulate matter buildup, increasing maintenance needs and potentially leading to costly repairs or replacements.
Key Takeaway: Impact of Driving Conditions
Driving conditions that prevent the truck from operating at conditions conducive to automatic DPF regeneration are particularly problematic. Highways or long-haul operations, where trucks can maintain consistent speeds, allow the engine to reach and sustain optimal temperatures for passive regeneration. In contrast, urban driving, with frequent stops, starts, and lower average speeds, does not facilitate this natural cleaning process, necessitating more frequent active regeneration cycles. These cycles can be fuel-intensive and may temporarily impact the vehicle's performance.
Tackling the Emissions Challenge
Understanding the limitations of passive regeneration in certain driving conditions highlights the importance of focusing on active and manual (or forced) regeneration processes to maintain the efficiency and longevity of Diesel Particulate Filters (DPF) and overall after-treatment systems. Both drivers and fleet managers play critical roles in this maintenance aspect, ensuring these systems operate effectively, especially in environments where passive regeneration is less likely to occur naturally.
Active Regeneration
Active regeneration involves the vehicle's onboard computer system initiating the burn-off of accumulated particulate matter in the DPF at lower temperatures than those required for passive regeneration. This process can happen while the vehicle is in operation and does not require the engine to be at full operating temperature. It's an automated response to soot buildup, but it does require the vehicle to be running at a certain speed for a specific duration, which may not always be feasible in stop-and-go traffic or during short-haul trips.
For fleet managers and drivers, understanding the conditions that trigger active regeneration and how to facilitate this process is essential. This may include planning routes that allow for the necessary operating conditions or scheduling driving patterns that enable the system to initiate active regeneration without interrupting daily operations.
Manual (Forced) Regeneration
When active regeneration is not sufficient to clear the DPF, or if the vehicle's use does not allow for regular active regeneration, manual (forced) regeneration becomes necessary. This process requires the vehicle to be stationary and is initiated through a command from a diagnostic tool or the vehicle's onboard interface, depending on the model and system configuration.
Fleet managers should train drivers on recognizing the signs that indicate a manual regeneration is needed, such as dashboard warning lights or reduced performance signals. Additionally, scheduling regular manual regenerations based on vehicle use and driving conditions can prevent the buildup of particulate matter to levels that could lead to DPF damage or failure.
Kenworth T470: Heavy-Duty Reliability
The Kenworth T470 is designed for heavier-duty applications, providing a bridge between the medium-duty trucks and the larger, class 8 vehicles. It's built for durability, but its heavy-duty nature introduces specific maintenance challenges.
Suspension and Alignment
Given its heavy-duty role, the T470 is often subject to harsher operating conditions than its T370 counterpart. This puts a lot of stress on the suspension and alignment systems. Regular checks and maintenance of these components are crucial to prevent premature wear and tear.
Components to Consider:
- Shock Absorberssome text
- Responsible for controlling rebound movement, shock absorption, and plays a significant role in the handling of your truck.
- Air Systemsome text
- Including your air compressor, airbags, levelling valves, etc.
- Leaf Springs some text
- In trucks without air suspension, leaf spring maintenance is an absolute must! Be sure to check your leaf spring hangers for rust, and keep an eye on the health of your bushings!
Did you know, problems with your suspension or alignment can lead to uneven tire wear, reduced handling, and increased fuel consumption?
Brake System
While the brake system in any vehicle is vital, in heavy-duty trucks like the T470, the stakes are even higher due to the vehicle's size and the loads it carries. The brake system must be regularly inspected and maintained to ensure it functions correctly. Wear and tear on brake components can be accelerated by the heavy loads and frequent use common in commercial trucking, leading to increased maintenance demands.
Components to Consider:
- Slack Adjusters some text
- Take up the slack when your brake shoes wear down.
- Service Chamberssome text
- Facilitate the air braking process.
- Air Systemsome text
- Air dryer, compressed air tanks, compressor, etc.
Training and Equipment
Investing in training for maintenance personnel is essential. Understanding the specific requirements and potential issues of the T370 and T470 models enables more effective troubleshooting and repair. Additionally, having the right diagnostic tools and equipment is crucial for maintaining these advanced trucks.
Utilizing Technology
Both the T370 and T470 are equipped with modern technology that can aid in maintenance. Telematics systems, for example, can provide real-time data on vehicle performance and alert fleet managers to potential issues. Leveraging this technology can help in proactive maintenance planning and execution.
Final Thoughts
The Kenworth T370 and T470 models are vital assets for businesses operating in and around Houston, Texas. While these trucks are built for reliability and performance, their advanced features and heavy-duty capabilities also bring specific maintenance challenges. By understanding these challenges and implementing effective maintenance strategies, companies can ensure their fleets remain operational, efficient, and safe on the road.
Investing in regular maintenance, training, and technology is key to overcoming these challenges and maximizing the lifespan and efficiency of these essential commercial vehicles.
More Articles
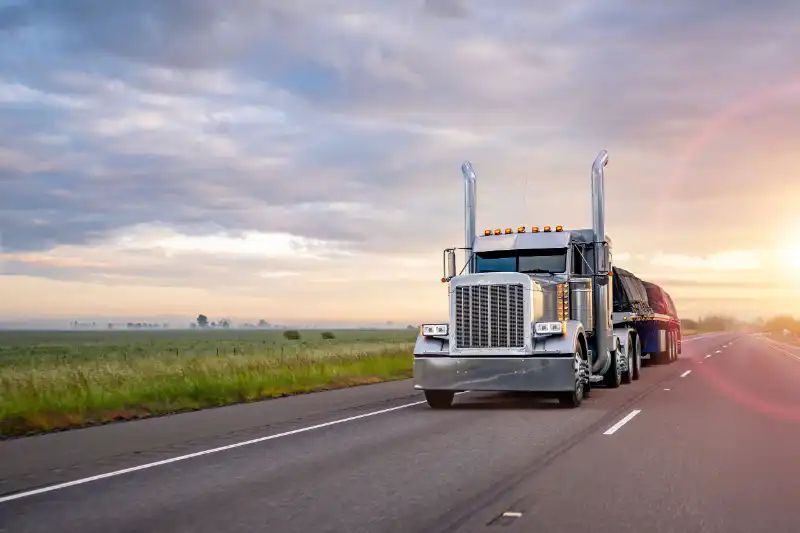
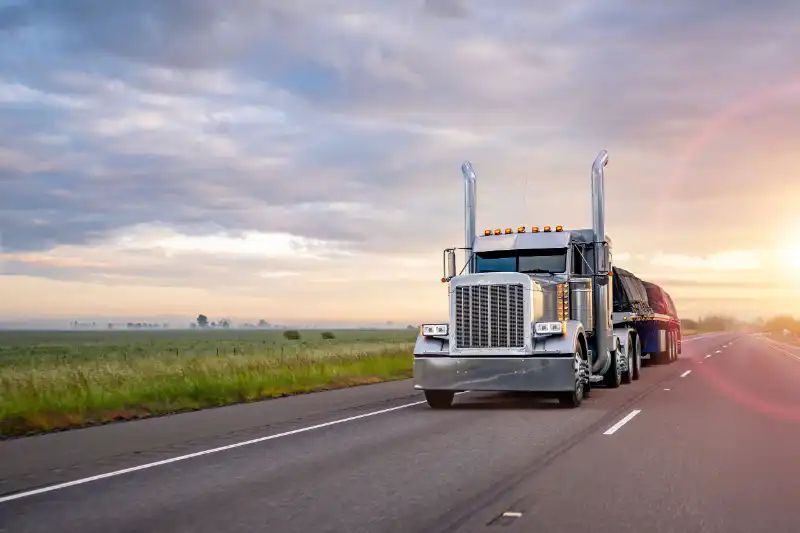
Top 7 Ways to Keep Your Grocery Fleet Running Smoothly This Summer
Top 7 Ways to Keep Your Grocery Fleet Running Smoothly This Summer
Prevent breakdowns and keep your grocery fleet running efficiently in summer. Learn how to protect engines, tires, refrigeration units, and drivers from extreme heat.
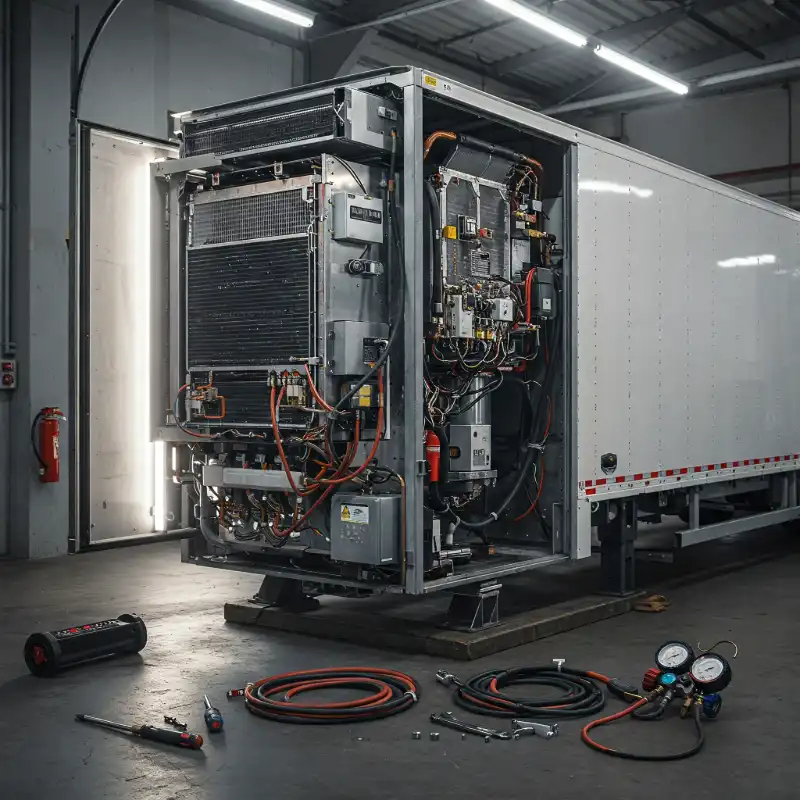
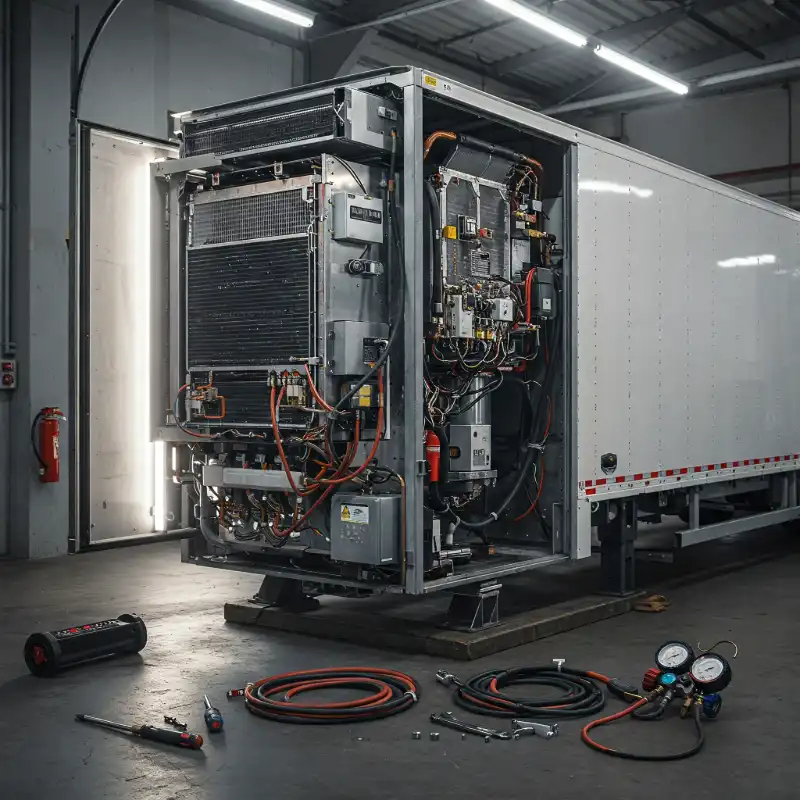
7 Errors in Refrigerated Truck Maintenance and Their Fixes
7 Errors in Refrigerated Truck Maintenance and Their Fixes
Avoid costly breakdowns and cargo loss with proper refrigerated truck maintenance. Learn about the top 7 reefer maintenance mistakes and how to fix them.
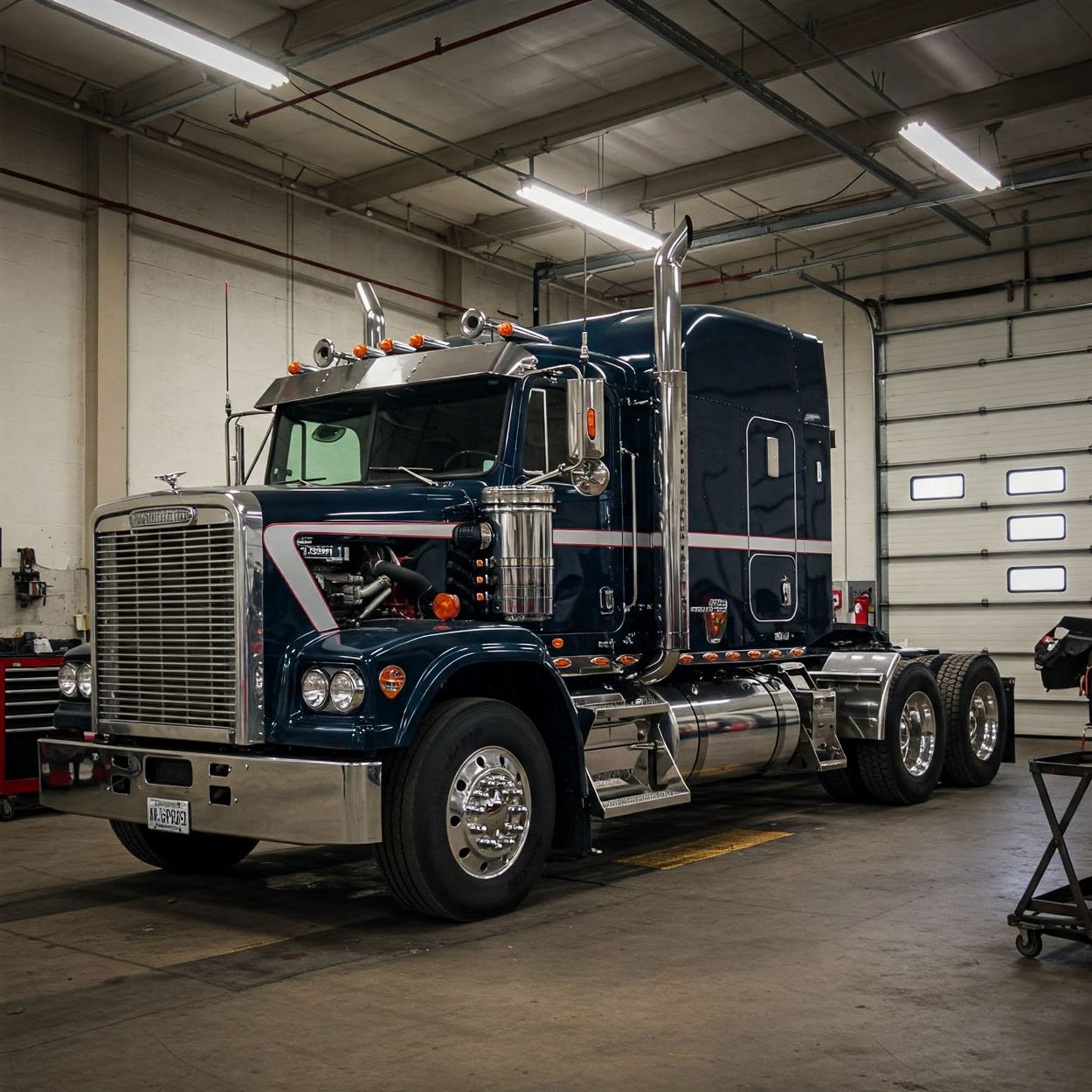
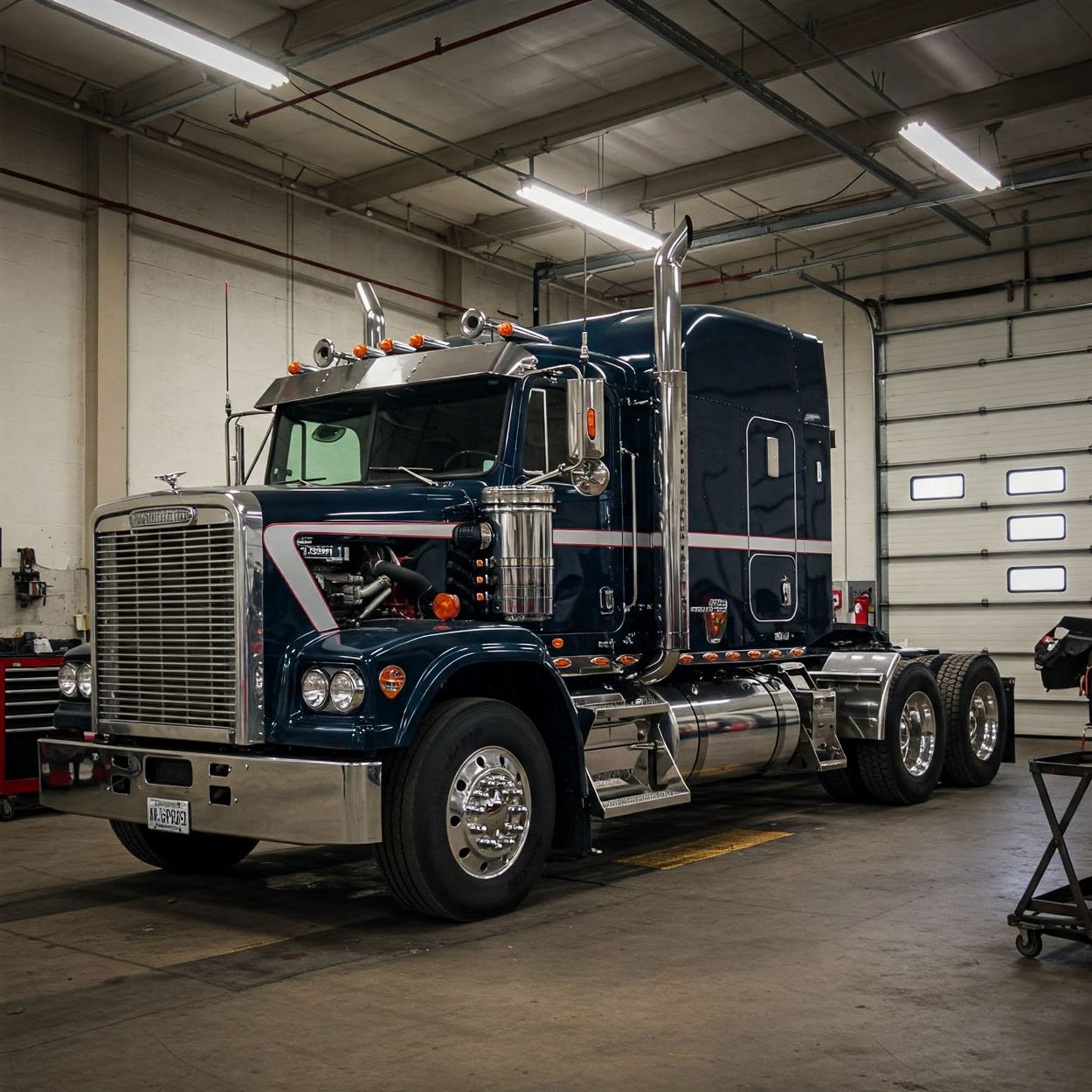
What Are the Benefits of Telematics in Managing Food Delivery Fleets?
What Are the Benefits of Telematics in Managing Food Delivery Fleets?
Discover how telematics can optimize your food delivery fleet in Texas. Reduce fuel costs, improve efficiency, enhance safety, and ensure faster deliveries with real-time tracking and smart analytics.